Celadon From Mengrai Kilns |
"Celadon"
is the commonly accepted name for kind of high-fired
stoneware with a wood ash glaze (usually crackled), which is
hand crafted by a traditional process believed to have been first
developed in China some 2,000 years ago. In Chiang Mai, the
glaze is usually made of silt from a rice field and wood ash
from a particular tree. The body of the pot is made of stoneware
clay (know as "din dam", literally black earth)
froma local deposit. When fired in a reduction atmosphere (high
Co2, low o2 content), the natural iron content of the glaze and
of the body combine to produce the delicate shade of green which
is associated with gook celadons. Too much oxygen in the kiln
gives different shades, varying from olive green through yellow
to brown. The glaze can be varied by using other kinds of ash
(i.e. rice stalk, bean stalk, or bamboo), and other clays.
|
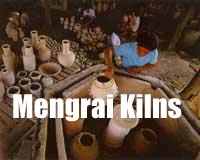 |
|
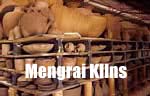 |
In the
final firing, the kiln must be taken to about 1,260C in order
to vitrify the glaze. The result is a bright transparent gloss
finish. The crackle (otherwise known as 'crazing') is caused by
a difference in the coefficient of contraction between the body
and the glaze when the pot is cooling. |
|
|
A brief celadon and stoneware production
process: |
2.1 The
dried stoneware clay is reduced to powder and sieved. It is then
mixed with water, passed through a pug mill to improve the
blending, and allowed to age for a while by bacteriological
action. 2.2 Before throwing on the wheel, the
clay is kneaded, to remove air bubbles and to improve plasticity.
2.3 After throwing, the pots are allowed to
dry until they are "leather hard". They are then often hand
carved, incised of embellished with a high relief applied
decoration. Thereafter, they are allowed to dry naturally in the
air. When quite dry, they are checked for cracks and defects.
|
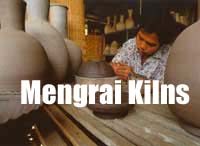 |
|
2.4 At this point, the pots are still
"green”. That is, they will revert to mud if put into a bucket of
water 2.5 The next step is bisque firing, in a
tub kiln, to about 800 C. Though stable in water, the bisque ware
pots are still porous. A second check for cracks and defects is
made
2.6 The bisque pots are then glazed, usually by
dipping in the glaze mix, and allowed to dry.
2.7 The final firing follows, to 1,260 C or
1,300 C in a reduction atmosphere, as already described. The pots
are again checked for defects, cracks or leaks. From start to
finish, the process takes about one and a half months. |
|
|
Why is it called "celadon"? |
|
One theory is propounded
by William Willetts in "Chinese Celadons and
Other Related Wares in Southeast Asia" (South-east Asian
Ceramics Society, Singapore, published by Arts Orientals,
Singapore, 1979). He writes: "There is moreover no reason to
suppose that the ware was known as celadon until the last years
of the 19th century…..(when)…the word 'celadon' was used to name
a colour,… of a costume worn by the shepherd Celadon in….the
17th-century pastoral romance L'Astree, by Honore d'Urfe… Not
until the 6th…edition of the Concise Oxford
Dictionary (1976) do definitions relating to ceramic
materials appear…namely (1) 'grey-green glaze used on some
pottery' and (2) 'Chinese pottery thus glazed'. "Willetts comments
that the Complete oxford English Dictionary (a much bigger work)
did not define celadon correctly until 1945- if I understand him
well - when it indicated that celadon denoted the "high fired
stoneware made at the Lung -ch'uan kilns in Chekiang province of
eastern China from Suang times onwards and, at various times
subsequently, at other factories in other parts of country and
abroad". |
|
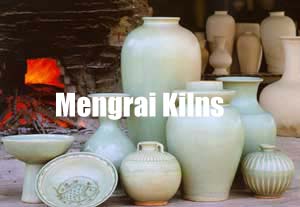 |
Turing
back to the publication by the Southeast Asian Ceramics
Society referred to above, we find an article
by Lu Yaw. He attacks the term 'celadon' as an
historical misnomer, and prefers the name "qing ci"
, meaning green or bluish-green porcelain ware,
(Romanized Japanese "seiji"). He then goes on to note that the
Ashmolean Museum of oriental Art (Oxford) and the Museum
Pusat (Jakarta) have discarded the term 'celadons, and
use "Chinese green wares" instead. He adds that the
Percival David Foundation of Chinese Art (London)
may be moving in the same direction. But he then tends to
destroy his own argument by saying that, in certain firing
conditions, these 'greenwares" may not be green at all, and may
even be 'yellowish or brownish". |
|
Here we would add that some green coloured wares,
for example those with a lead based copper glaze fired in
oxidation, can certainly not be regarded as celadons. And
finally, a practicing potter calls a "green pot"
one which has been thrown and air dried, but not yet bisque
fired.Consequently, we prefer to agree with Willetts. He does
indeed ask why one should use a word of European derivation
(celadon) "to name the product of a Far Eastern potter when the
Chinese term 'ch'ing tz'u' is lying at hand”. He answers his own
question by saying that celadon' conjures up and image of this
class of proto-porcelain in all its beauty, whereas the other
term |
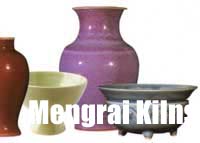 |
|
does not. He speaks
as a Westerner and we are Asians. All the same, we prefer'
celadon. Everybody the world over who likes pots clearly
understands what that means, and has an instant concept of this
unique art form Anyway, what's in a name? Let us enjoy the visual
and tactile pleasure pleasure of these unique pieces, and be
grateful to the old potters long dead who taught us how to make
them for our delight, and that of generations still unborn.
|
|
How long will the craft persist in its present
form? I hesitate to guess. But I fear that before long one will
not be able to find the raw materials needed for making celadons
in the traditional way. And what of the essential loving skill of
the artist craftsmen who so proudly sing each
Mengrai pot they make to day? We can pass on
our craft to our children: but cannot be sure that it will be
there for our grandchildren to inherit. Perhaps this thought puts
the value of Mengrai hand crafted wares in better perspective.
|
|
|
|